How to Manage Supermarket Warehouses Receiving Process in 2022
Warehouse receiving management involves the transfer of ownership of goods and ensuring that the documentation is accurate, smooth, and efficient, ultimately making the products available to the customer as soon as possible. No matter how extensive your supermarket business processes are, it begins with receiving stock.
If the receiving process is properly done, the rest of the supply chain will run smoothly. If errors are allowed to slip through, every other process step will be impacted. Optimizing your supermarket warehouse receiving process will offer your business tons of benefits and save you a lot of stress and issues.
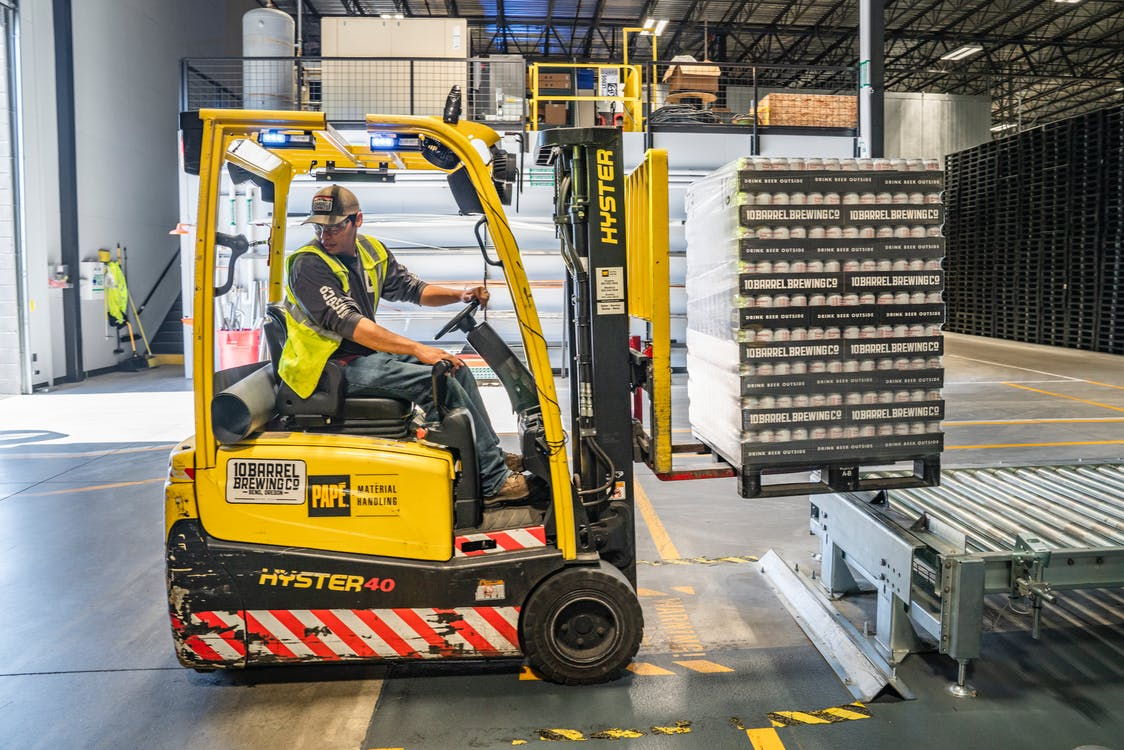
Main challenges involved in the warehouse receiving process
1. Low traceability and connectivity
Low traceability and connectivity lead to loss of control over the goods and the continuity of the supply. This problem may occur when you fail to know the product's status from order processing through inventory management at any point in the supply chain (e.g., during processing, packaging, warehousing, and dispatching).
Your brand image will receive a negative impact when some low-quality or fraudulent products are seen in your supermarket. Customers are satisfied when they are confident of getting every information about the product they need. Traceability helps track the original product in the supply chain and thus avoid product counterfeiting.
2. Inaccurate inventory and outfitting
Warehouse inaccurate inventory is a critical aspect. This challenge can cause errors in customers' orders, a shortage of products, theft, damages, and even loss of your business. Most inventory problems occur from inadequate control measures and a lack of proper reporting for transactions happening in real-time within the warehouse.
Proficient warehouse receiving processes will have better order and demand management, less labor effort, more on-time deliveries, and optimal use of space and equipment.
3. Delays in the gathering process
Delays in the gathering process mostly happen when items can't be found in suitable locations. If a product is not where it should be in the warehouse, the picker needs to spend extra time gathering. This delays the order fulfillment, leading to unhappy customers and negative reviews. On top of that, it also makes for highly inefficient warehouse management.
The gathering process also determines how easy it will be for you to stock the shelves when new products arrive. Frequently picked items should be readily accessible, while low-demand items should be taken out of the way. You may need to re-organize the floor of your warehouse seasonally to accommodate changes in product demands.
4. Damaged products
One common challenge for supermarkets is product receiving damage. Damaged goods are just as good as lost items. Replacing damaged good expenses are usually much higher than the original cost. Your business does not only lose the money it had put in, but it also has to spend more to handle that loss. High amounts of damage can indicate a bigger problem of poor safety measures and calls for instant action.
Solutions for supermarket warehouse receiving process
1. RFID fast reading capability
RFID is one of the solutions to the challenges of a supermarket warehouse process. RFID (radio frequency identification) is a wireless technology that uses radio-frequency electromagnetic fields to transfer data. Tagging items with RFID tags allow you to automatically and uniquely identify and track inventory and assets. Large data can be collected, transferred, checked, and updated fast without errors such as faulty scanning, miss scanning, or re-scanning. Additionally, RFID allows for batch scanning of over 50 items at the time and long-distance readings. Overall, warehouse items can be easily located as all product movements are tracked, and this information is automatically registered in the system.
2. PDA more accurate items pick up
Portable warehouse PDA (Personal Digital Assistant), also called a handheld terminal. It is a barcode scanner designed for data collection and scanning. You can use PDA to quickly scan and query goods and send the information to the database so that the management can understand the sales situation of each store in real-time. PDA dramatically improves the efficiency and accuracy of inventory and inspection, which helps avoid a shortage of goods. Moreover, mobile computers' rugged nature is especially suitable for use throughout the supermarket supply chain as they are resistant to shocks and drops.
3. Real-time visibility
Real-time visibility in supermarket warehouse management has become highly essential. It allows you to trace and track the movement of goods and packages from the suppliers, warehouses, and hubs to the end customer. With real-time visibility, you can know what is happening per time and also be able to rectify the problem by ascertaining the situation and finding the best solution on the spot. This action helps to decrease costs, conserve working capital and improve efficiency.
4. Handling of damaged products
As packages are transported, they are exposed to possible damage. You must inspect your products before signing your proof of delivery. PDA solutions such as mobile computers and tablets can take photos of the products as they are being offloaded. Those photos can act as proof in the case of legal issues. Ultimately, mobile computers offer many other functions to assist workers in their daily operations, such as GPS and vocal communication.
Conclusion
In addition to the solutions mentioned above, using tools like industrial mobile computers would go a long way in improving the warehouse receiving process of a supermarket. Mobile devices allow you to scan new inventory and accurately store information quickly.
Under these circumstances, supermarkets can use Urovo's DT50U RFID handheld reader. With its built-in 5dBi high-sensitivity RFID antenna, the DT50U can read RFID tags within 20 meters in large quantities. The equipment supports unpacking and inventory even with objects obstructing the field of vision.
Interestingly, the device comes with a built-in dual PA and a longer Wi-Fi transmission range, significantly reducing the enterprise's network deployment costs. Equipped with a Qualcomm octa-core 2.2GHz processor and powered by Android 9, the device has a 16MP camera that records on-site emergencies, offering workers superior operation and data durability.
Contact us! Learn more about our solutions and find the right one for your unique needs. We are ready to assist you!